Semi-Autonomous Mobile Robot: MEAM 510 Final Project (Penn 2021)
This final project is the culmination of MEAM 510: Design of Mechatronic Systems in my first semester of the Robotics MSE program at the University of Pennsylvania.
The purpose of this robot was to compete head-to-head with other student bots in an end of semester competition, which required bots to move cans into their respective scoring zone. Most of these cans broadcast their X-Y position in the arena over Wi-Fi via UDP packets; however one can on each side of the field, the highly-valuable “beacon”, emitted only IR pulses. The reason these cans broadcast these signals is because each team’s driver is unable to see the enemy’s half of the arena. To be competitive, our team thus needed to implement semi-autonomous behaviors relying on several sensing modalities in addition to responsive and nimble movement. The majority of our robot’s functionality is controlled by an ESP32 microcontroller which is Wi-Fi enabled.
To track our X-Y position on the field we created an IR photodiode circuit which could sense, condition, and amplify signal received from an HTC VIVE Base Station which was installed above the competition arena. We then duplicated this circuit and placed the two sensors at the front and back of the bot. This enabled us to find our orientation and then apply some simple vector math and proportional gain for steering to autonomously navigate to a given position (e.g. can location). We also implemented range sensing to perform wall-following. Using two ToF sensors placed on the front and right sides of the bot, we were able to achieve autonomous counter-clockwise movement around the perimeter of the field – great for entering and remaining inside enemy territory. To track the beacons, we created another IR detection circuit with high amplification which could detect the beacon pulses at 23 and 700Hz. This required two IR phototransistors, each with a narrow cone of detection, such that we could drive the robot to spin about itself and move forward when both sensors read the appropriate pulse at the same time.
The motor circuit includes two wheels controlled by two H-Bridge drivers and an inverter which handles digital output from the ESP32 to specify direction. Motor speed is determined by a PWM signal whose duty cycle can be actively set by the driver. Ultimately, all functionality, including toggling autonomous behaviors, is controlled over Wi-Fi via an HTML interface.
My responsibilities in this project included: soldering all boards, designing the motor driver circuit, designing the beacon detection circuit, building the VIVE circuit, solving navigational vector math, and pair programming with a teammate to integrate all functionality on the ESP32. (NOTE: I elected to focus on electrical design and programming, as I felt already familiar with mechanical design)
For more information including circuit schematics, see our Final Project Report here: Team40_FinalReport
Remote-driven performance in the Final competition:
Moving to UDP broadcast can position in competition arena:
Beacon tracking:
Wall Following:
Pick and Place Challenge: MEAM 520 Final Project (Penn 2021)
The MEAM520 final project was a “Pick and Place Challenge” to reliably grasp both stationary and dynamic blocks and stack them on a goal platform, right-side up, in as tall a tower as possible.
The competition occurred in a shared environment between two teams. Each team has access to two platforms in front of the arm, one for the static blocks and one for the goal (scoring zone). The four static blocks were randomly dispersed on a stationary platform while the dynamic blocks were placed around the edge of a rotating turntable. Both teams shared a single dynamic block turntable and the pool of dynamic blocks. Scoring was based on the type of block placed, it’s altitude, and its orientation – with higher scores for dynamic blocks, higher altitude, and right-side-up block pose.
My team advanced to the finals of this competition after three successful group stage rounds; however, we experienced an error in the final and needed to withdraw. Still, this competition was an incredible experience in which I was able to employ forward kinematics, inverse kinematics, path planning algorithms, offline computation, and more which was covered throughout the semesters.
My responsibilities in this project include: deriving the transformations and processing strategy to convert from a simulated vision system data to usable block poses, developing static block stacking strategy, building offline IK solver as separate python class, and optimizing our final script.
First Static Stacking Test:
Static and Dynamic Stacking (not yet optimized):
AR Helmet Tracking – Computer Vision: CIS 581 Final Project (Penn 2021)
CIS_581__Final_Project_Final_Report
Google Drive folder with Final Presentation, Final Jupyter Notebook (open via Google Colab), and Output Videos:
Electromagnetic Clamp Design: ECE 535 Final Project (NCSU 2020)
As a final project for ECE 535: Design of Electromechanical Systems, a graduate course taught by Dr. Gregory Buckner, students were tasked with designing an electro-permanent magnetic clamp (EPMC) that could be used to immobilize a metal work-piece during the machining process. The benefit of EPMCs is that they require no power draw in either ON/OFF configuration, yet still achieve strong clamping forces on ferromagnetic materials. They rely on both rare earth (AlNiCo) magnets and weaker ceramic magnets that can flip polarity to switch between clamp ON and OFF states. The ultimate goal was to maximize ON configuration clamping force while keeping OFF configuration forces below a certain threshold.
My team, comprising three undergraduates and one graduate student, worked remotely to develop an EMPC that far surpassed the minimal requirements and featured a robust technical analysis and report. My responsibilities included modeling the system in FEMM (a free finite element electromagnetic modeling software), and developing a methodology to select the attributes of the electrical and magnetic system required to switch between the two clamping states.
Final comments from Dr. Buckner included:
- “Very impressive use of analytical and computational methods… Overall, very thorough and correct technical aspects. I’ll be surprised to see a more comprehensive project than this… excellent!”
- “The aforementioned technical methods… were novel, impressive.”
The full technical report can be accessed here: Design Project Report
Instructor Evaluation: MAE-ECE 535 Design Project Grading Grant 99
SafeCrate (NCSU 2020)
In the United States, households with a pet have come to outnumber those with children, and there is a market trend towards higher spending, especially on pet health products. It is also reported that nearly half of all dogs experience anxiety, many cases of which are caused by loud distressing sounds. As a part of the NC State Engineering Entrepreneurs Program (EEP), my team worked to develop a dog crate that provides a quieter and more acoustically-stable environment for pets which creates more relief than current products. Our product, SafeCrate, effectively addresses the root causes of noise anxiety, yielding a novel product that will undoubtedly attract pet owners. SafeCrate is an enclosure that utilizes Passive Noise Cancellation (PNC) and noise masking technology to limit the effect of distressing ambient sounds on pets.
Initially, our team intended to primarily rely on Active Noise Cancellation (ANC) technology not unlike what is commonly being implemented in state-of-the-art headphones and the cabins of several new lines of vehicles. We even created our own analog ANC signal-inverting circuit during the earlier prototyping phase, but found it to be ineffective at canceling sound uniformly in an open volume. This type of system was promising because it works exceedingly well for low frequency sounds such as fireworks and thunder which are the most notorious distressing sounds for many pets. However, a more effective digital ANC system run by a microprocessor would be exceedingly complicated and could realistically double production costs for the crate. This, along with research indicating that noise masking could provide adequate relief to animals, led the team to cease development of an ANC system in favor of the less complicated and more effective noise masking solution.
The team shared responsibilities in all areas, from researching the engineering principles involved to intensive market research. However, I was responsible for creating all graphic and video content, as well as final design and primary CAD modeling of our finished prototype MVP.
Our full Technical Report can be found HERE: SafeCrate Technical Document
Our Market and Competition Analysis can be found HERE: SafeCrate Market and Competition Brief
Final Prototype (created virtually due to campus closure response to Covid-19)
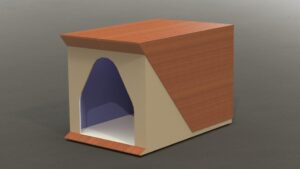
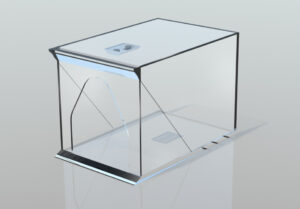
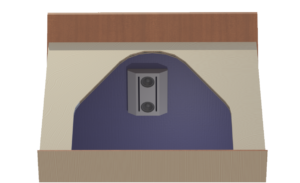
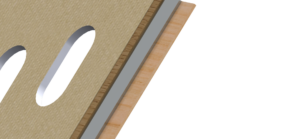

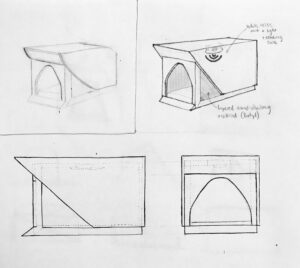
The noise masking unit is visibly integrated into the ceiling of the crate, and emits soothing white noise via an analog white noise circuit. The design is centered around modernist design and meant to integrate well into a home interior, as opposed to wire crates or other garish options. lastly, the walls feature a sandwiched layer or high-density, noise deadening butyl.
First Prototypes
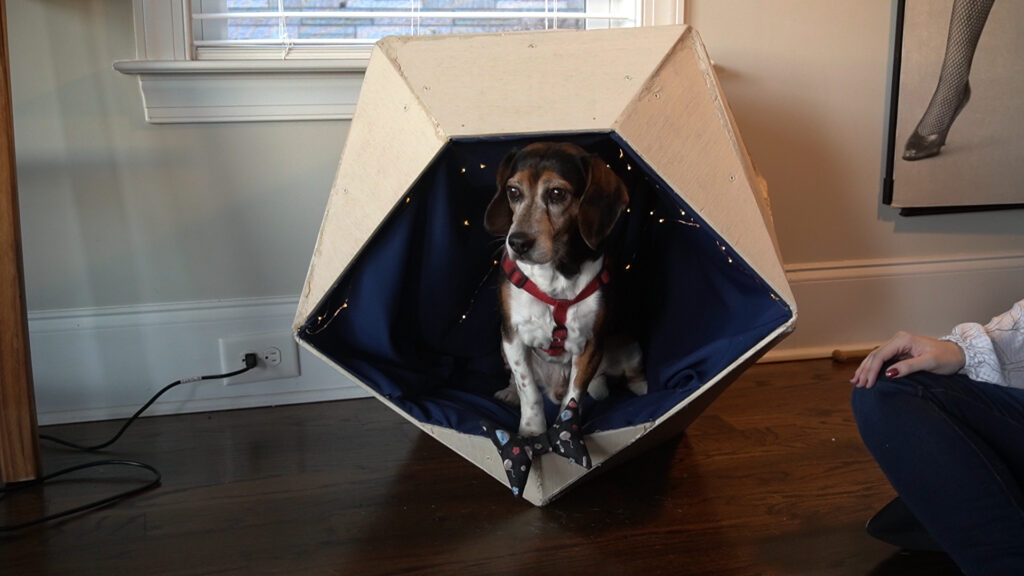
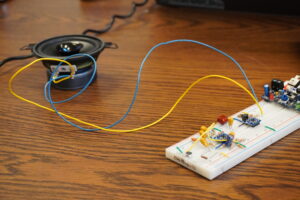
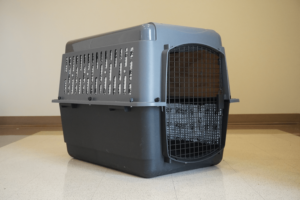
Make-a-thon (2018)
Make-a-thon is a “hack-a-thon” inspired competition hosted annually by the NC State Sustainability Office. Participants have only 48 hours to ideate, prototype, and pitch their sustainable product venture. The final pitch is performed on stage for all participants, event organizers, and judges. This served as my introduction to entrepreneurship at NC State, and allowed me to practice communicating technical information to a large audience.
My team and I ultimately created an internet-enabled home air filter quality detector that alerts a homeowner when filter replacement is required. This device would take the guesswork and forgetting out of replacing air filters, which would inevitably lead to significant long-term energy savings and promote the health of HVAC systems which are costly to repair. Our proposed venture included not only the physical device, but additional functionality to automate filter replacement through a subscription service that would ship new filters directly to the user.
Our prototype was created using a microcontroller with a custom light sensor to roughly determine the progression of particulate buildup on the surface of the filter. a user would be notified via a mobile application if the sensor value reached a certain threshold. While we did not place at this competition, we were met with an overwhelmingly positive response from judges and Sustainability Office staff. One facilities manager at NC State even approached our team and congratulated us for arriving at a novel idea which he felt could be implemented to great success at not just the residential scale, but even industrial applications such as the university.
Lightning Detector Module Design (NCSU 2017)
I was fortunate to have been able to pursue study abroad in Hangzhou, China in the summer of 2017. While there, I took an introductory electrical engineering course on circuits. As a part of this course, we partnered with a regional Caterpillar facility to design a lightning detector module for use in heavy machinery like backhoes. The device would ensure that an operator be warned of lightning strikes in the area and be able to take proper precautions and avoid risky behavior.
I led the physical design effort within my team, and created several CAD prototypes of the unit using SOLIDWORKS. The final design featured housing for the electrical components and a 9V battery, as well as an LED indicator panel and piezoelectric transducer for an audible alarm system. At the culmination of the course, we pitched our systems to the engineering team at the facility.
The actual lightning detector circuit (not pictured) included a band-pass filter to detect electromagnetic spikes in the signature frequency range of lightning strikes using a coiled antenna (located within the top of the unit).
Pencil Sharpener Upgrade (NCSU 2017)
I identified a common problem with most static, handheld pencil sharpeners. Pencil lead will often break off inside the chamber, rendering the sharpener useless until the graphite is painstakingly removed with a sharp object or brute force. It’s a small annoyance, but a problem all the same. I was just starting to regularly use SOLIDWORKS and I wanted more experience, so I attempted to model a system that could augment existing sharpeners to greatly facilitate the lead-removal process.
My design fits to the bottom of a sharpener and includes a covered spring-loaded button which, when pressed, sends prongs into the sharpening chamber to dislodge lead. This project allowed me to innovate while also further developing my modeling skills with a relatively more complicated assembly with some unique interlocking geometries.